Proactive vs Reactive
Crash cushion repair can take up to several months, an unacceptable timeline for lifesaving infrastructure. This product gives survey crews the tools to take initiative and fix units as soon as possible by keeping tools and consumables close by.
Expert Guidance
Faheem Seyed has over 25 years of experience in traffic engineering working with Cal-Trans.
While sharing my initial concepts with Mr. Seyed we talked about how to design crash cushion units better while, where innovation lies in traffic infrastructure, and, how to estimate the attenuation potential of concepts.
In my discussions, Mr. Seyed shared with me a different design shortcoming of the current crash cushion designs, the failure of proper logistical preparedness.
This new insight pushed me to design a system of repair and readiness.
Designing a system of Preparedness
Rather than waiting on lengthy logistics and procurement operations, this designs enable survey crews to take the initiative and proactively repair damaged crash cushions as they are spotted.
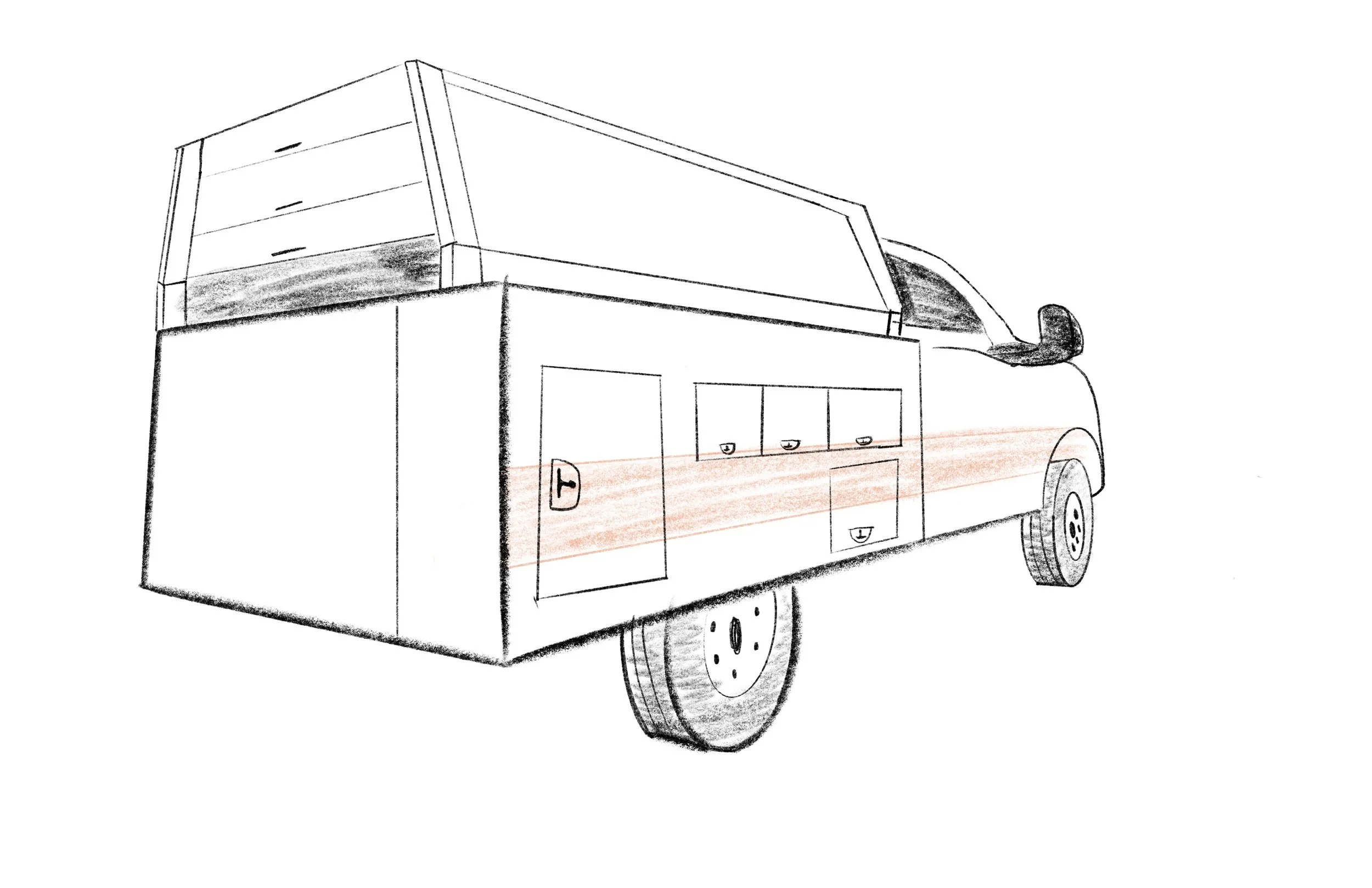
horizontal over head drawers with lower body utility cabinets
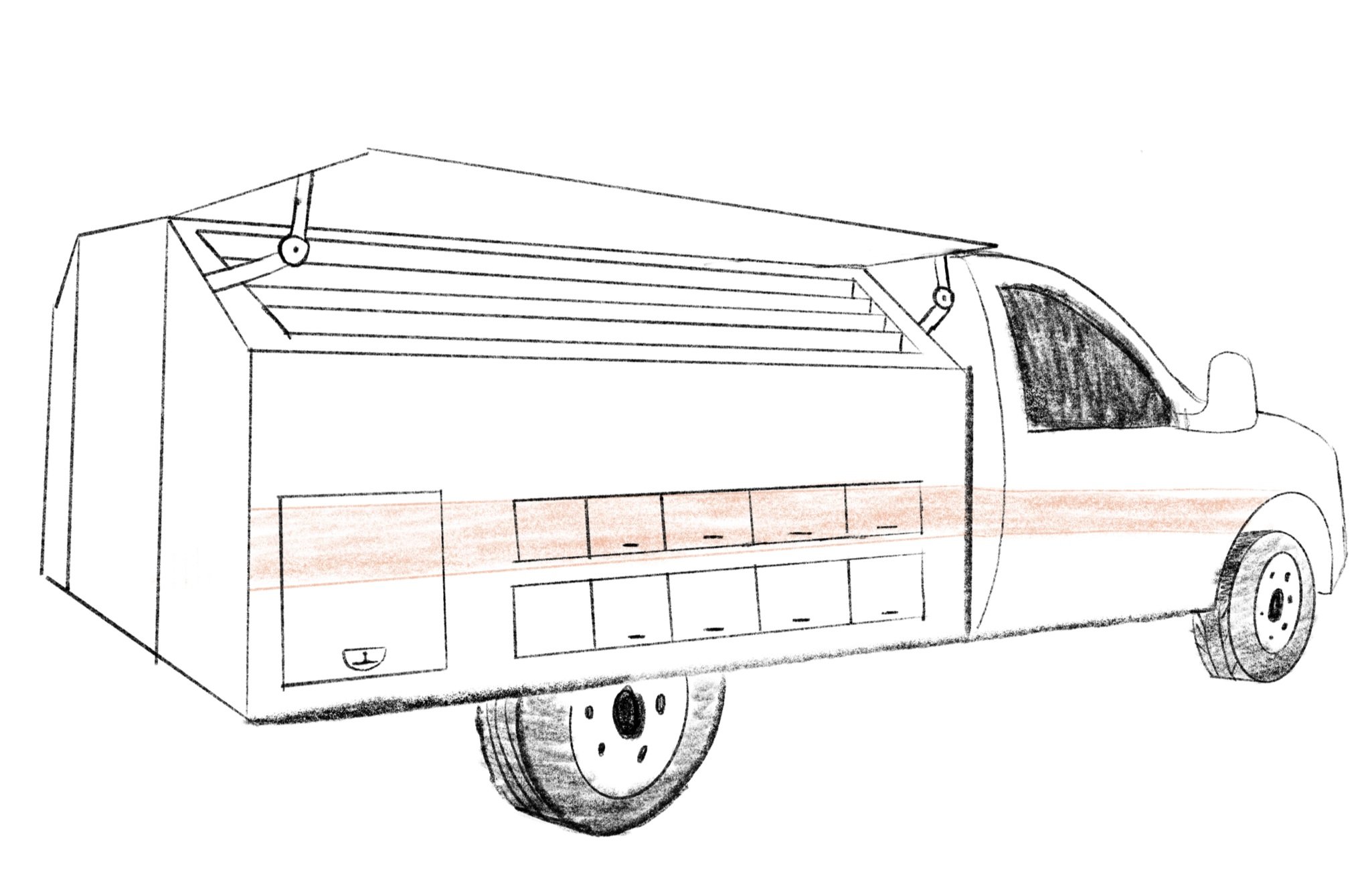
Vertical panel storage with lower body utility cabinets
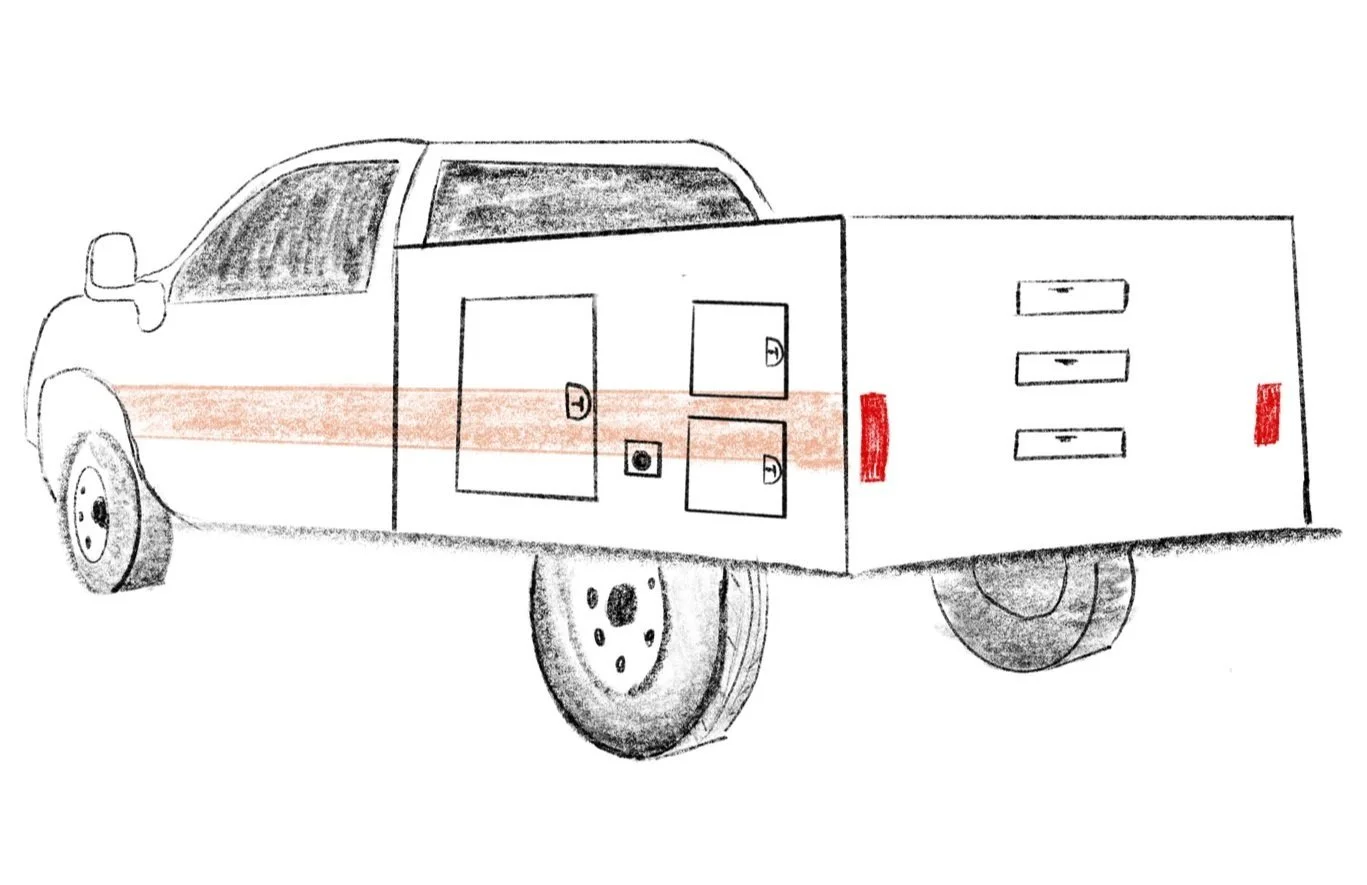
In-bed panel storage
Designed to get more work done faster
Survey crews operate out of Ford F-550 vehicles
Designed with consideration to the things you need the most
Wing nut washers
*not to scale
Validation Through Ergonomics
1:1 Scale model of a typical ford F550 utility body

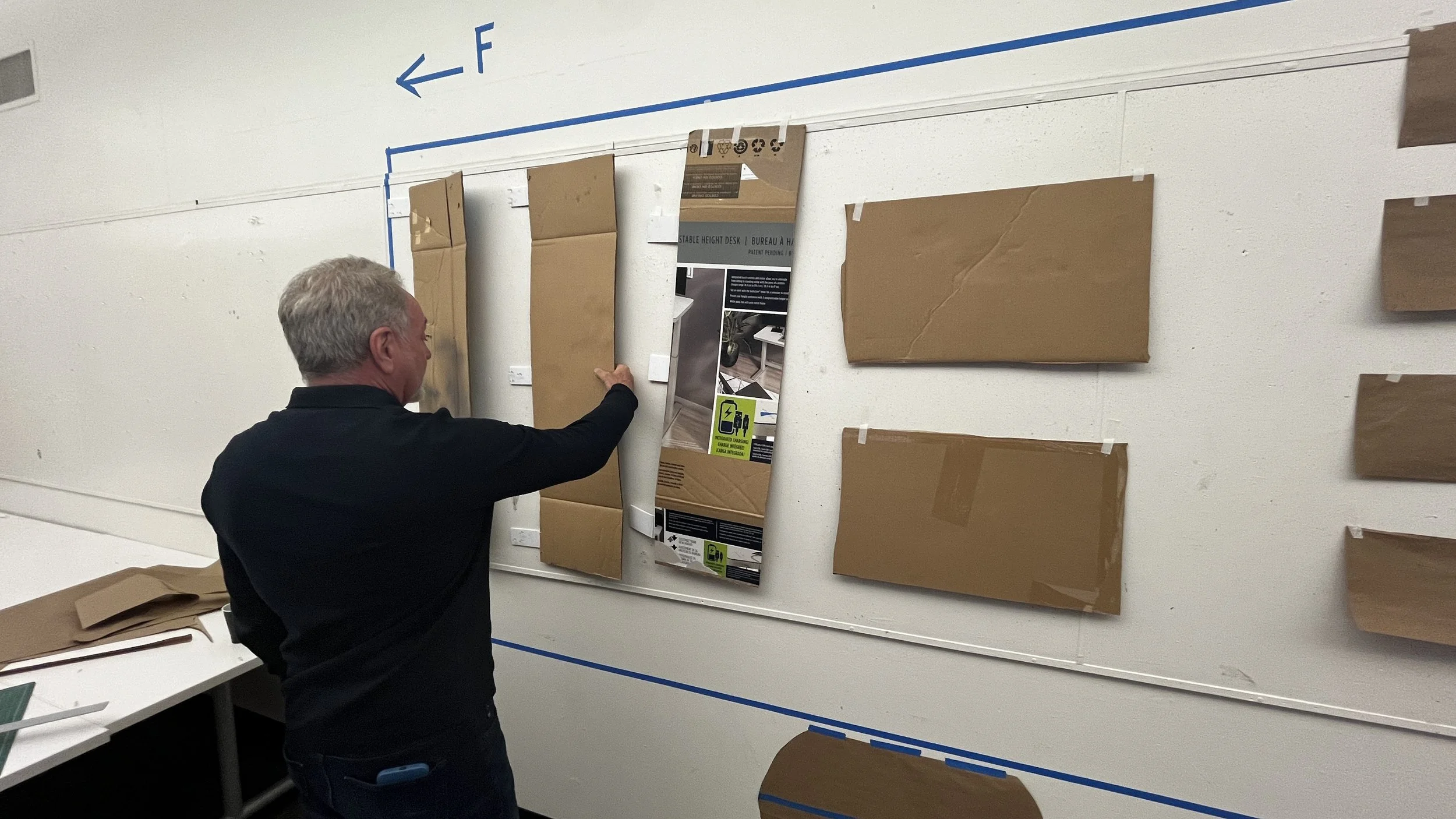
Making it Real
1:20 scale model
Acrylic, foam core, and 3D-printed construction
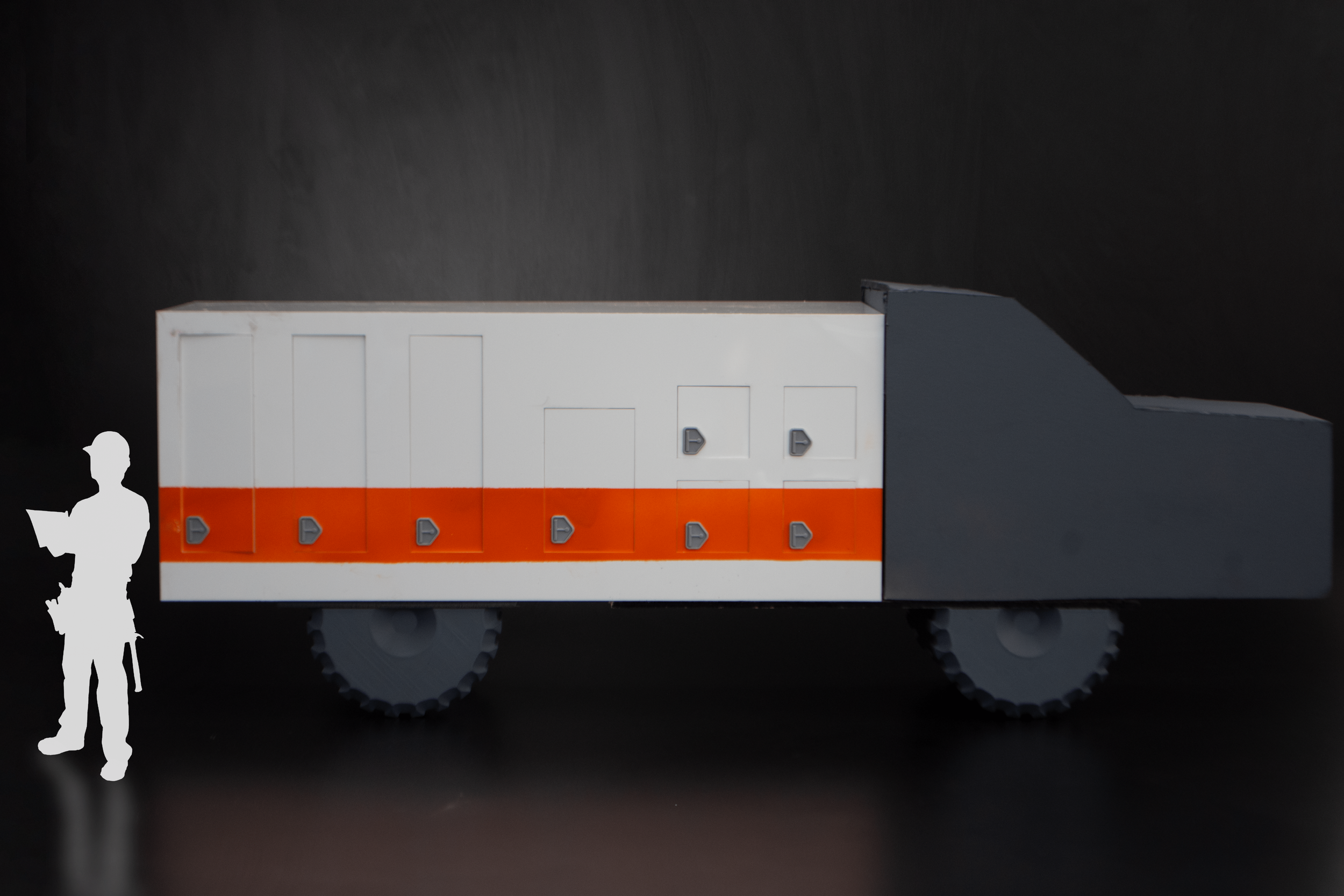
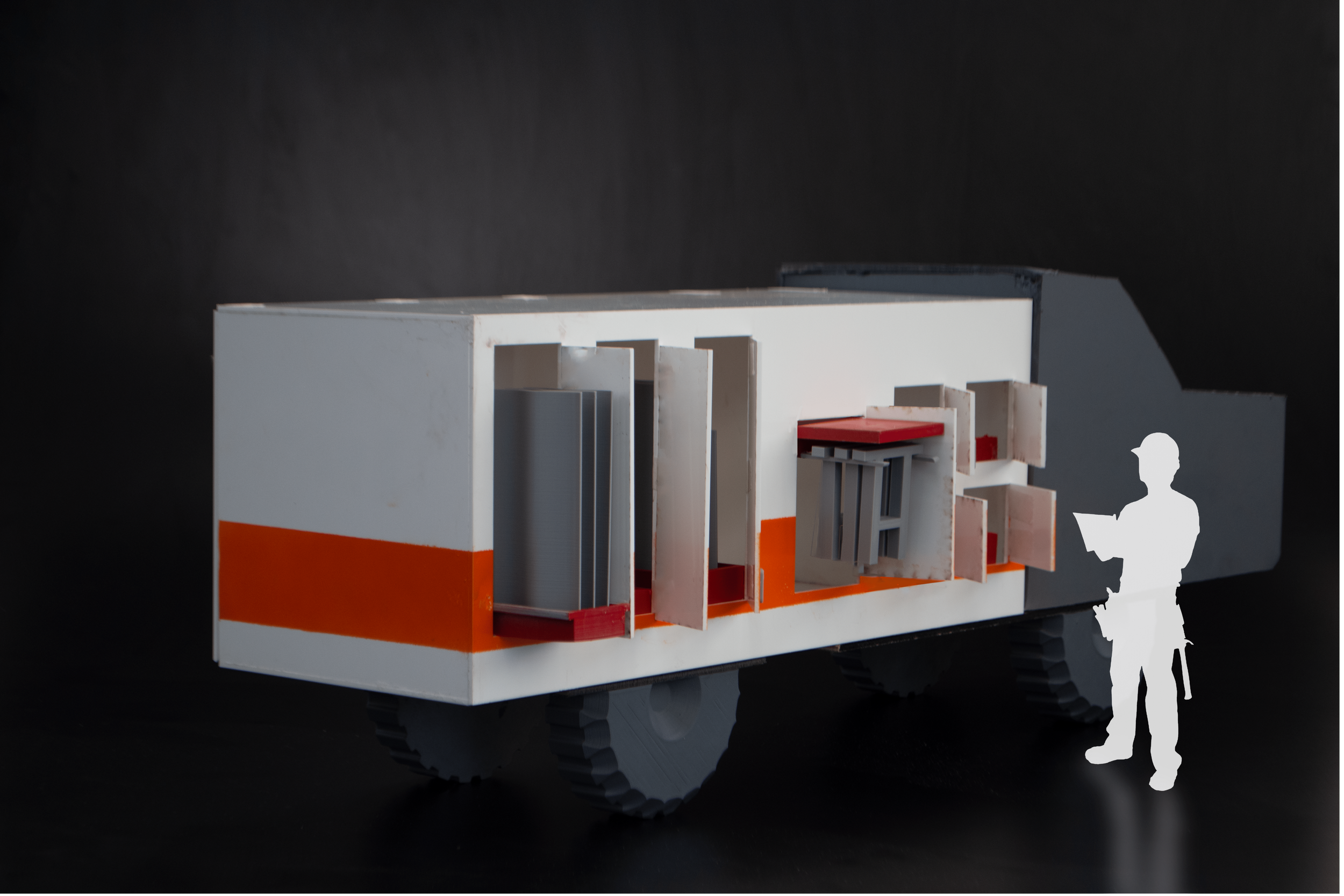
Maximum Productivity
