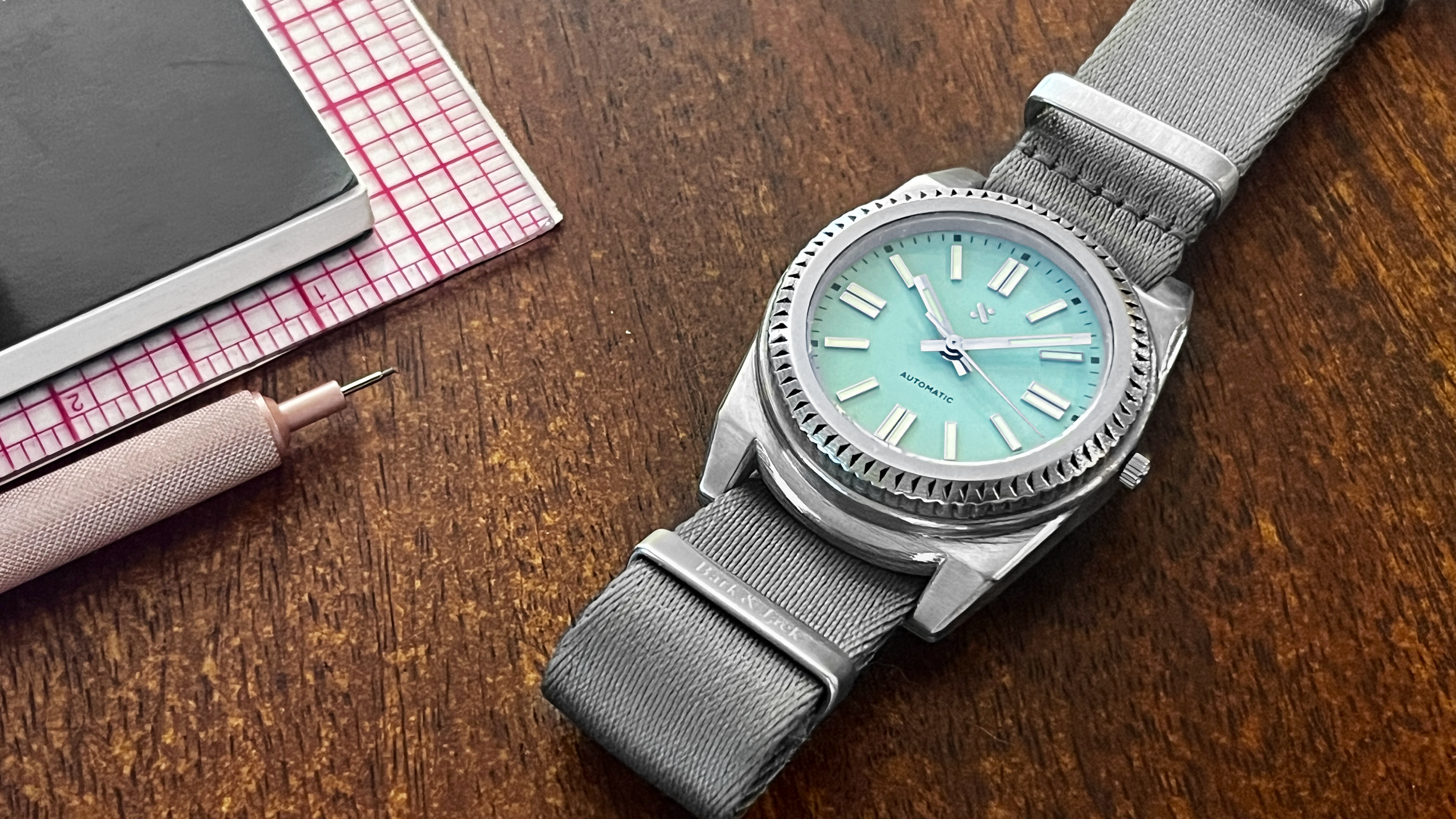
3D print a watch
In the luxury watch industry, brands are embracing novel manufacturing methods like Grade 5 titanium, forged carbon fiber, and tegimented steel to stand out and attract discerning consumers. Binder jetting technology (BJT) further advances this trend, offering new design possibilities leveraging the strengths of additive manufacturing processes. This innovative approach marks a shift towards more creativity and precision in watchmaking.
tegimented stee
Learning to play with the light
grade 5 titanium
forged carbon fiber
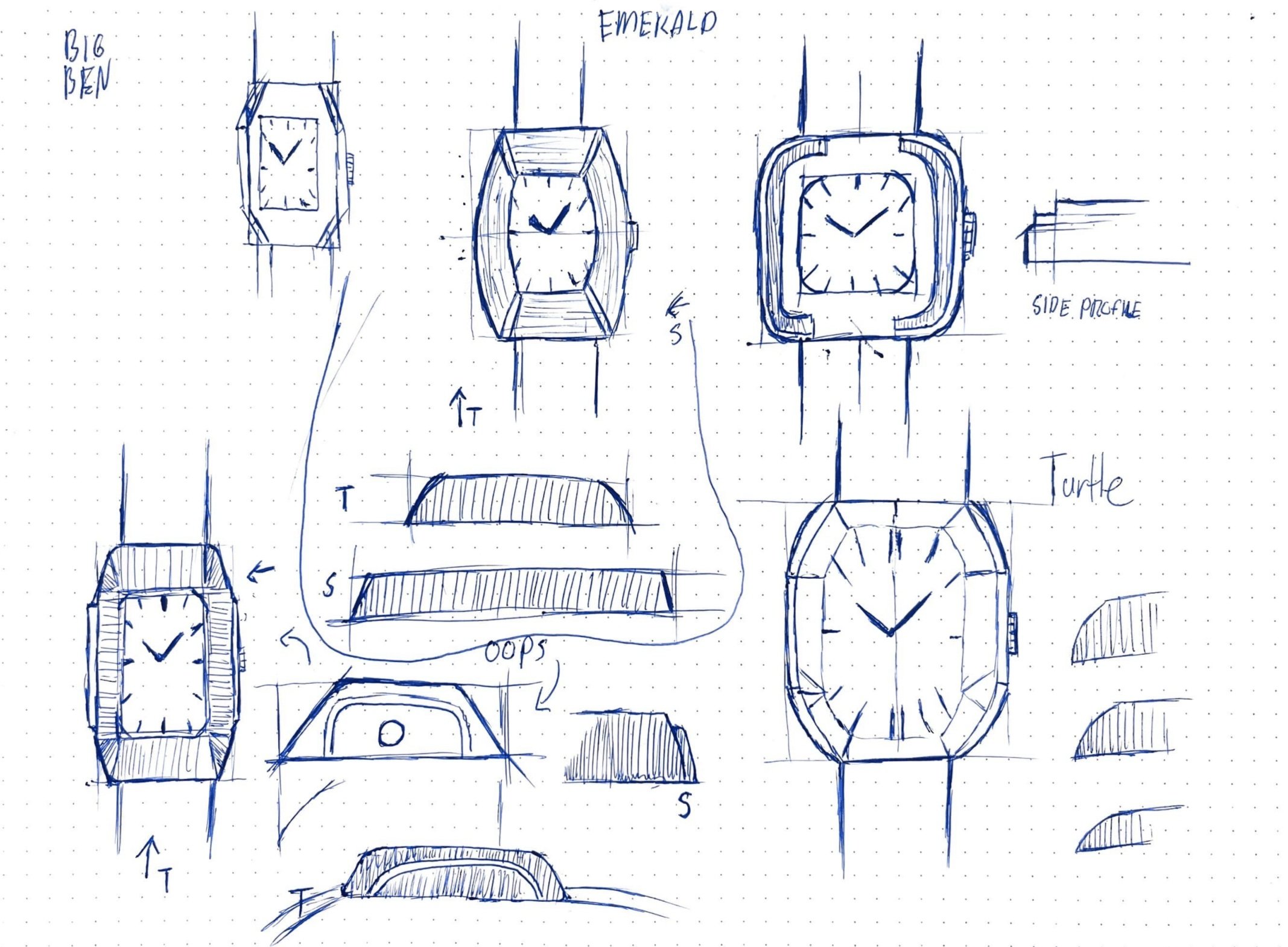

An Inspired Sports Design
With a “go anywhere do anything” energy
Leveraging the Process
At the heart of this design philosophy lies the deliberate inclusion of acute chamfered and straight edges, not only for their aesthetic elegance but to further extend the design vocabulary of modern-day watchmaking.
Through this strategic focus, I aim to deliver a product that not only meets but surpasses expectations, showcasing the transformative potential of additive manufacturing in contemporary watch design.

70 Points of Perfection.
In project Mainspring, I’ve focused on every detail, crafting a bezel with 70 precisely arranged triangles. Traditional CNC methods can't achieve those sharp inside edges. With additive manufacturing, we're able to bring intricate designs to life with precision and style.
High Horology… Low Costs
The most coveted qualities of a watch echo the refinement of fine jewelry or luxury automobiles. Features that only ones with an eye for detail will notice.
These features, often labor intensive and reliant on manual skill, include achieving sharp filleted edges on acute or 90° angles. By integrating 3D printing, production time is reduced, unlocking new design possibilities once deemed impractical at a large scale.
Mainspring utilizes 3D printing to achieve these features at a significantly reduced cost.